Today I machined the neck to it’s final shape (not the neck profile that is). I started out by cutting the neck well around the traced outline with a new jigsaw blade:
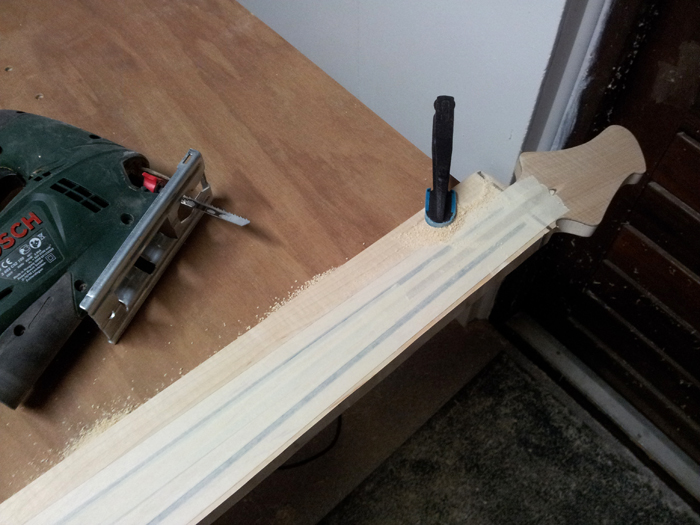
When done patiently and careful, this can’t go wrong, producing the rough shape of the neck:
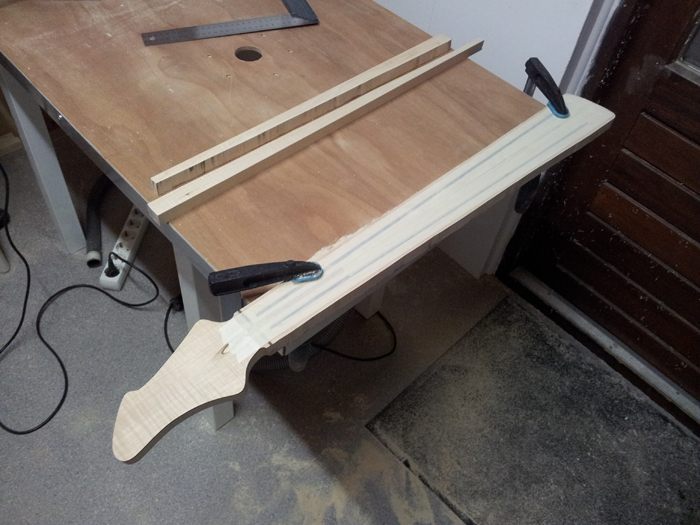
After that I aligned my neck template and started routing. I did not tape the template to the neck, because once the tape sticks it’s hard or impossible to do minor adjustments, so I clamped it in place. Here I’m almost done routing:
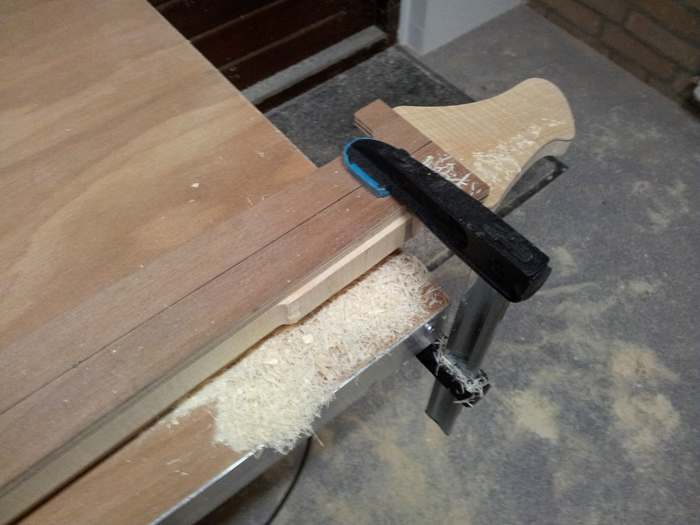
As you can see, the protrusions of the neck template pretty much explain themself right here. I also benefited from a well made template, because the neck to headstock transition is almost perfect after routing already, as I spent a lot of time to get the neck template and headstock template fitting together perfectly:
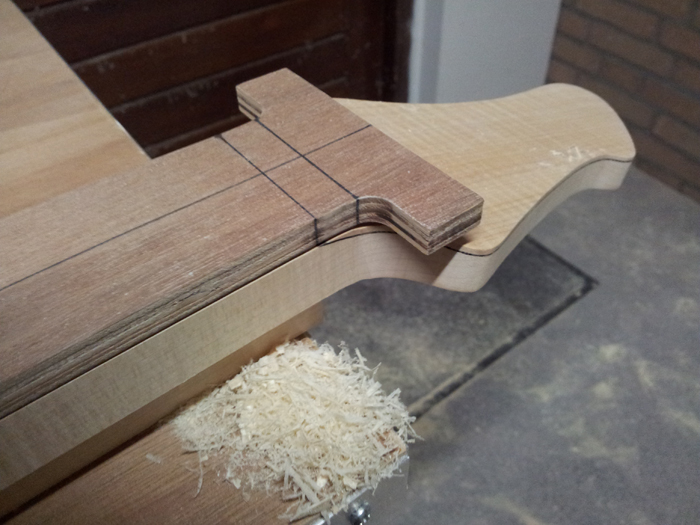
After routing, this is what I got left:
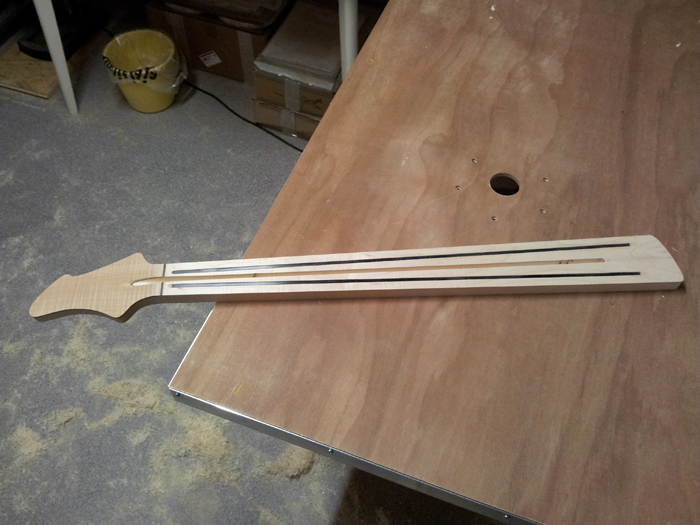
Here you can see the other side of the transition and.. I’m happy that I got some flames left, as they appeared mostly outside the outline of the neck shape:
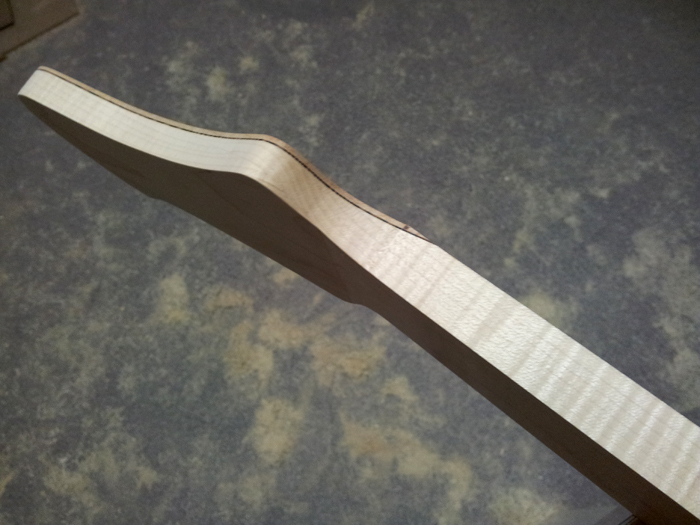
Did everything went well? No, sad enough, it didn’t. I had one very minor tearout where I stopped routing and started again after repositioning my clamps. That’s when I probably hit the grain in a delicate spot and got this:
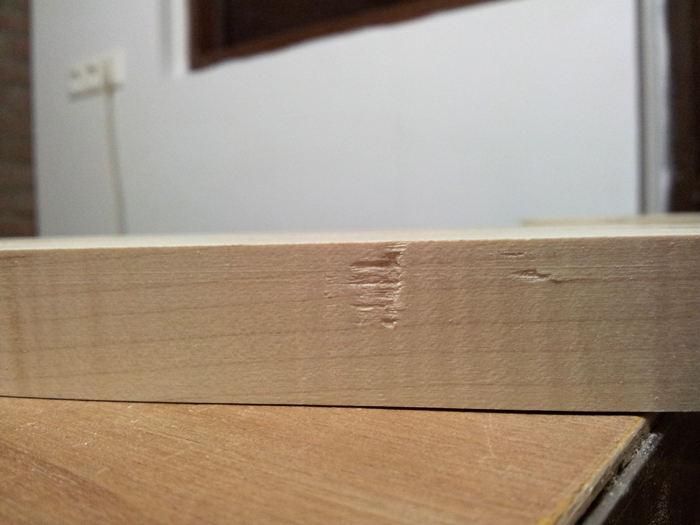
So I dug into a pile of sawdust and wood chips and I think I’ve found the concerning wood chip, so, after some negotiation I found it willing to get the hell back where it belongs
This is what we’re waiting for right now:
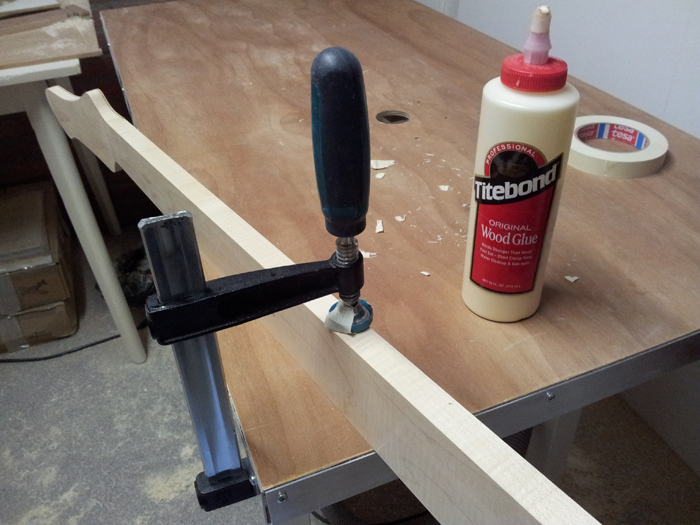
Since I will bind the fingerboard and the neck will obviously be shaped, I guess most of the wood where the tearout appeared will be removed anyway, but just in case, I want to get this fixed before I proceed. Chances are good it will be invisble in the final product…