Currently still busy with sanding parts (laser cut edges need sanding for better gluing) and laminating parts:
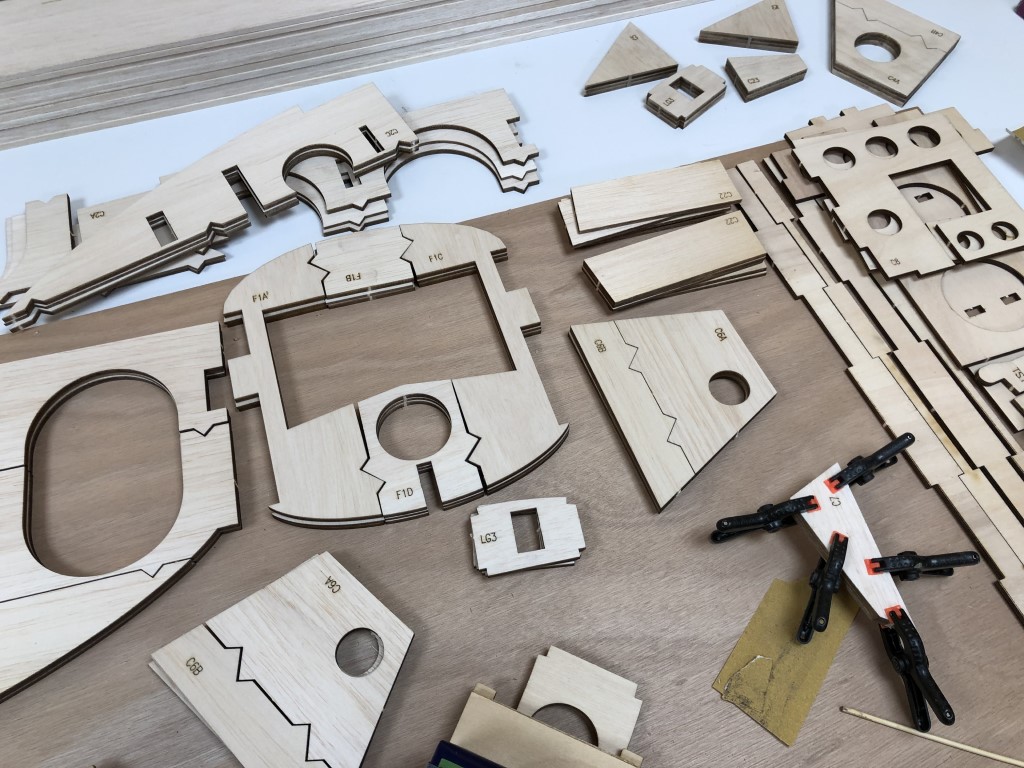
It took a while to find the right technique, but I think I’m there now. Stacking laser cut parts asks for accuracy. Here you can see a part built up out of three layers. Came out very clean and straight (please note that the final kit will not require laminating these parts, this is only due to some changes during the prototyping phase):
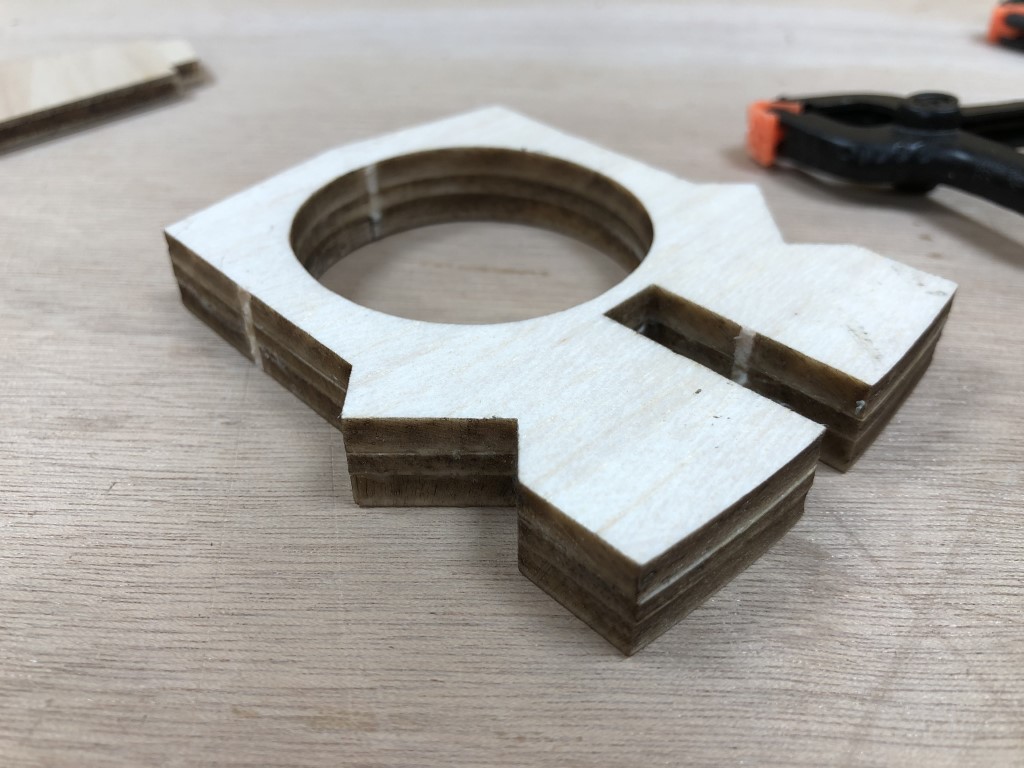
The next step is to join the stacked parts. Turned out it is very difficult to get a precise fit on those Z-joints. And I don’t want to sand too much, because in the end that would make the whole part smaller… this is a about the best I could get:
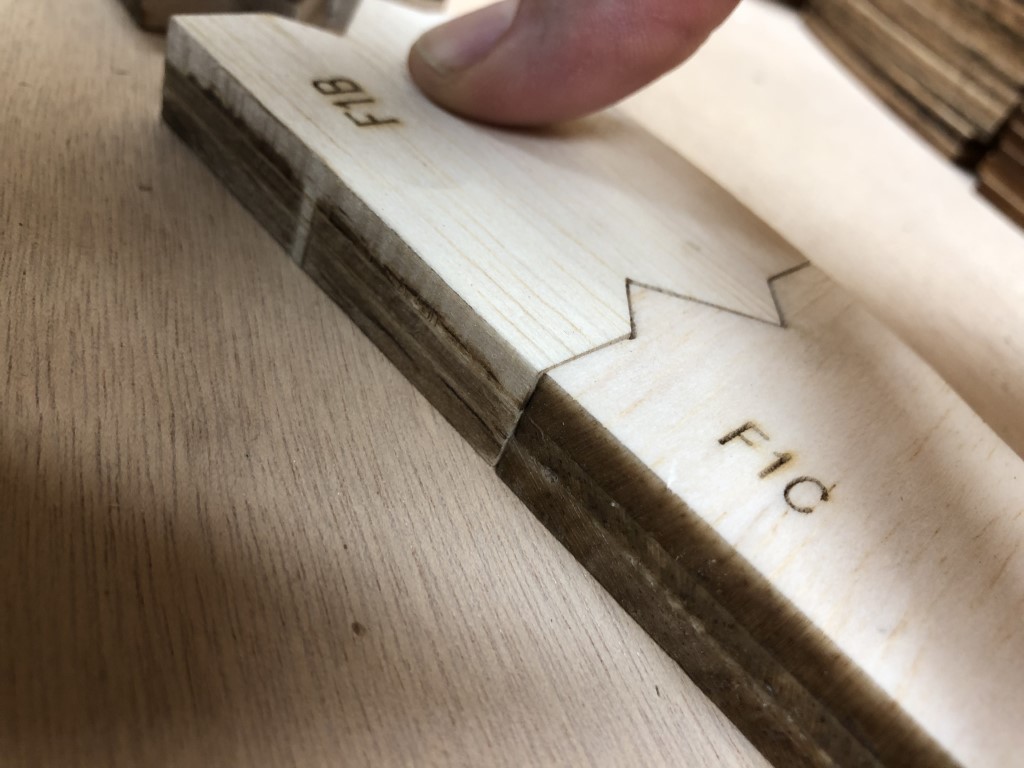
My preferred glue is aliphatic. But you need a good fit for that. So I decided to go with Bison PU Max for these joints. That glue foams a bit and is lightly filling, so it would make up for the not so precise fit. Turns out that was a great choice, because it even penetrates the balsa as you can see in this pic… it traveled all the way from the joint through the pores of the balsa, creating a very strong bond:
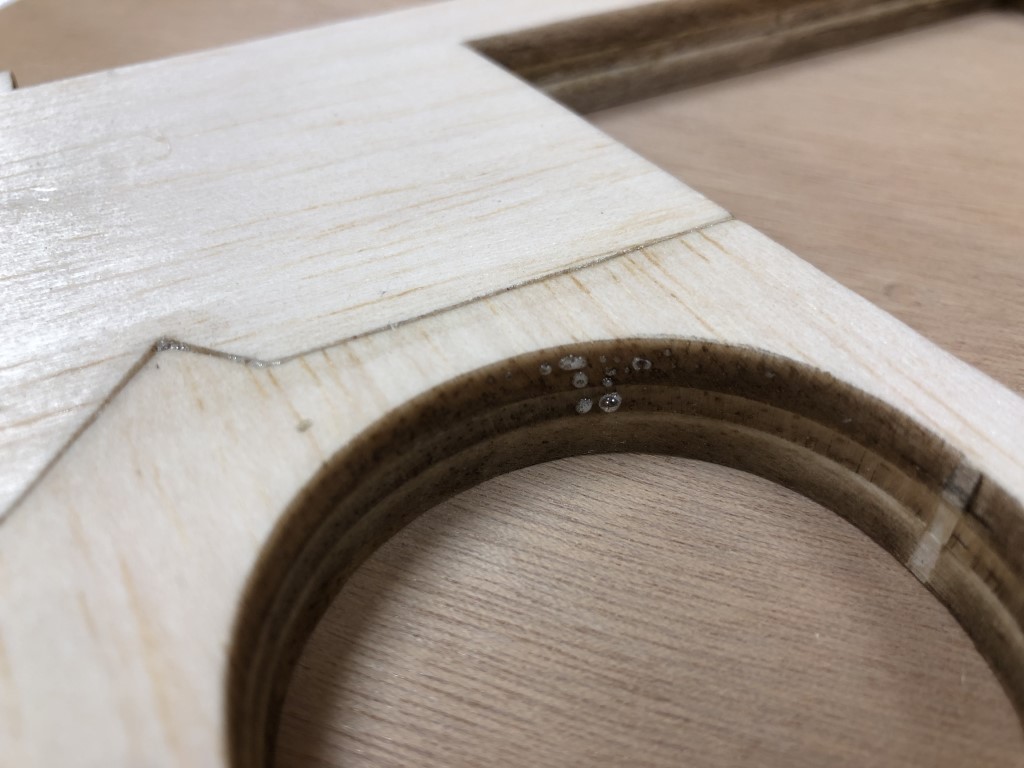
After sanding the contours, this is the end result. A strong and light former, that came out as straight as I could’ve hoped for:
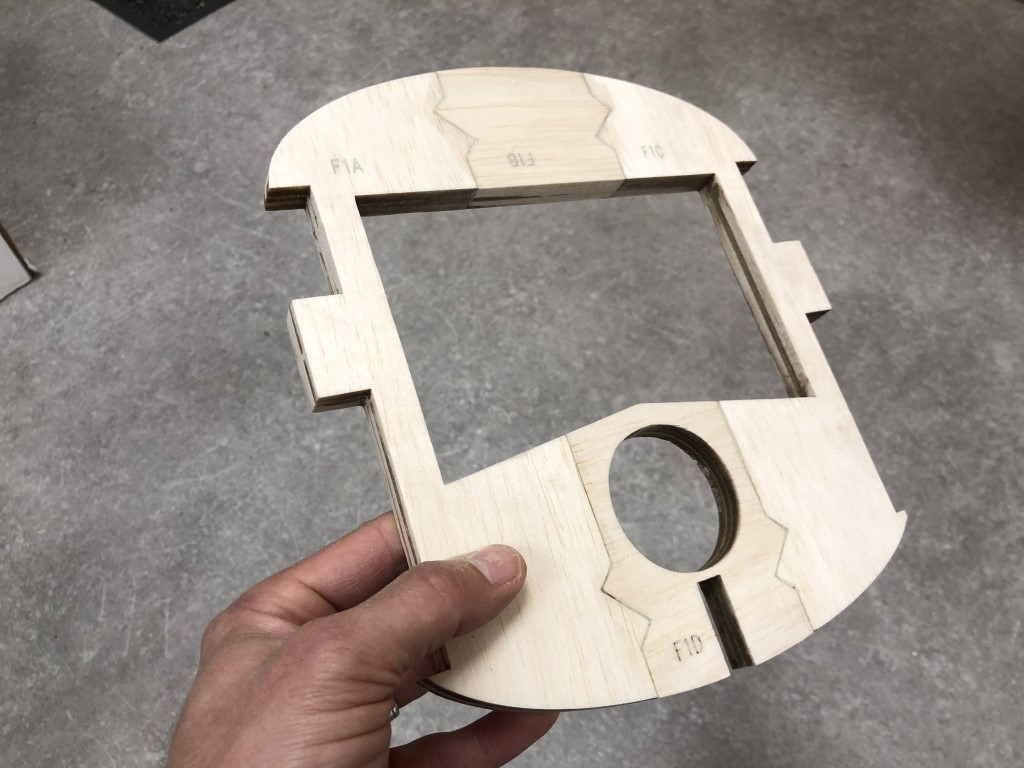
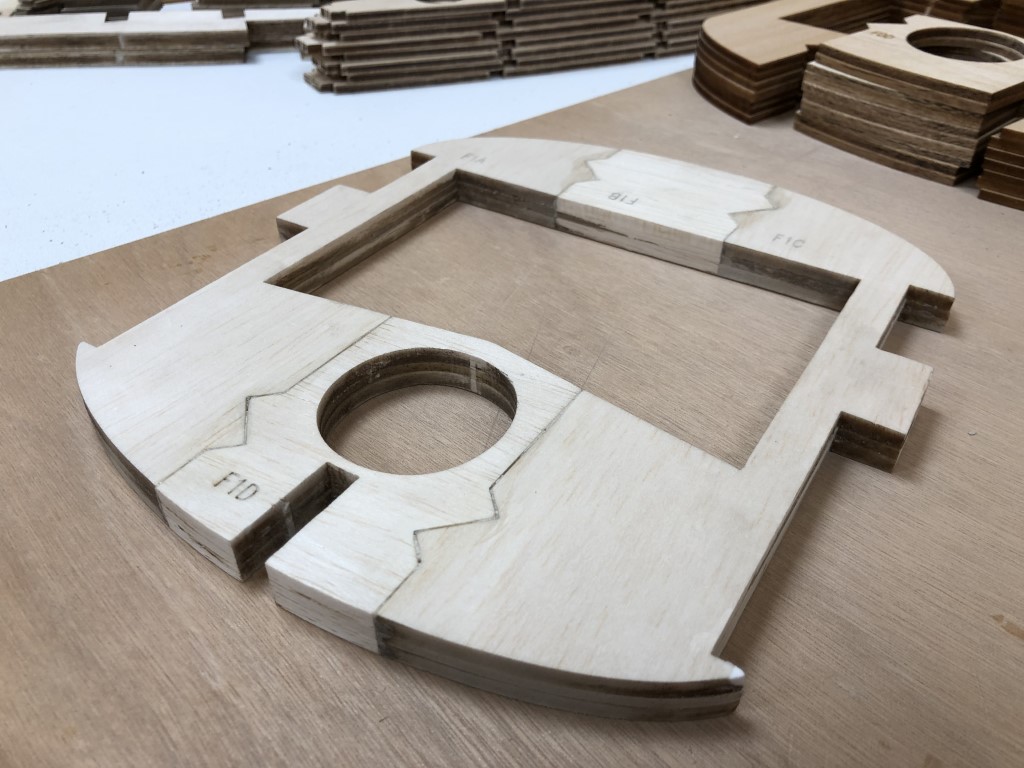
I still need to assemble former 0 and two fuselage cockpit sides. And during the curing of the glue, I’m sanding the cut out parts that don’t need to be assembled first. Already looking forward to starting the real construction of the fuselage, but I’m enjoying this part just as much :).