The next step is to design and build the custom muffler. I’m going with a simple design, I hope it will be effective and that it doesn’t create too much back pressure. From what I got from experienced builders I think this could work. At first I planned filling the chamber around the perforated tube with steel wool but I’m told that will clog with oil residues over time, so I’ll leave that out. Let’s see how this plan works out!
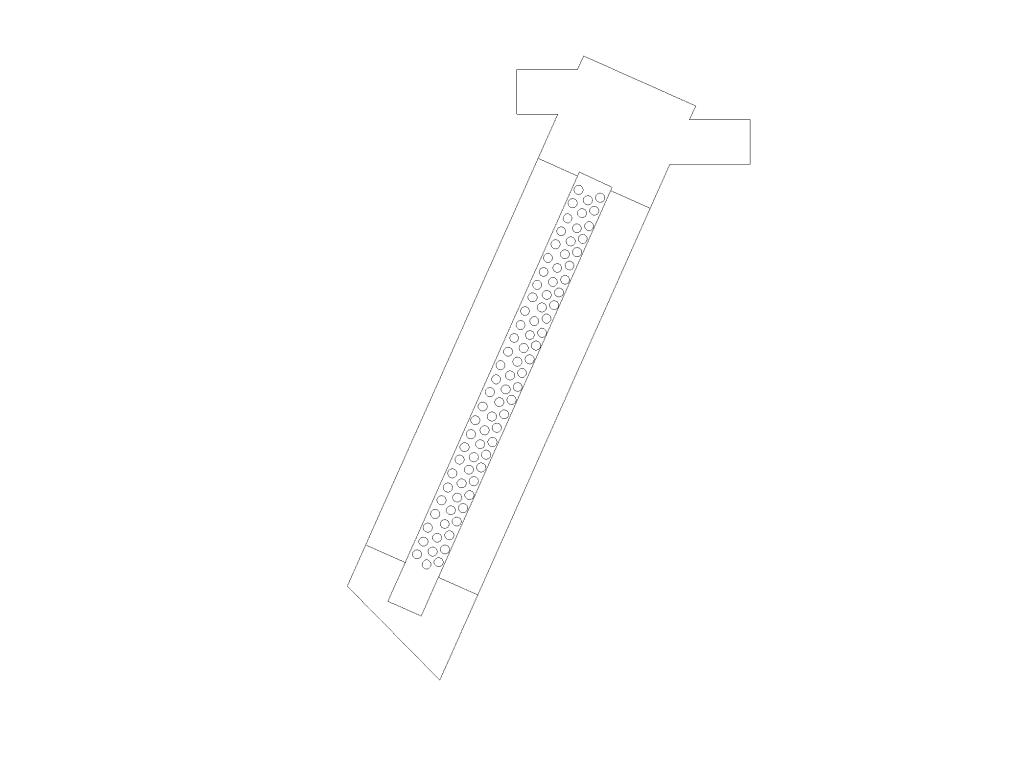
The muffler will be made entirely of stainless steel. Thin-walled perforated tubing is hard to come by, so I ordered a thin-walled tube with a diameter of 15 mm and a thickness of 0.5 mm. I drew a template in CAD and taped it around the tube to drill the perforations myself. Easier said than done. I did expect the tube to deform, so I put a 14 mm thick spruce rod in it, but it got stuck by the burrs from drilling into the steel… also, a 4 mm drill bit turned out to be too thick and a 2.5 mm bit didn’t bite / slipped away. My solution was to mark all 230 holes lightly with the 4 mm drill bit and then puncture the steel with my 2.5 mm bit afterwards. Then, I removed the wooden core by drilling it out from the sides with a 12 mm wood drill, before cleaning up the inside of the tube with a file.
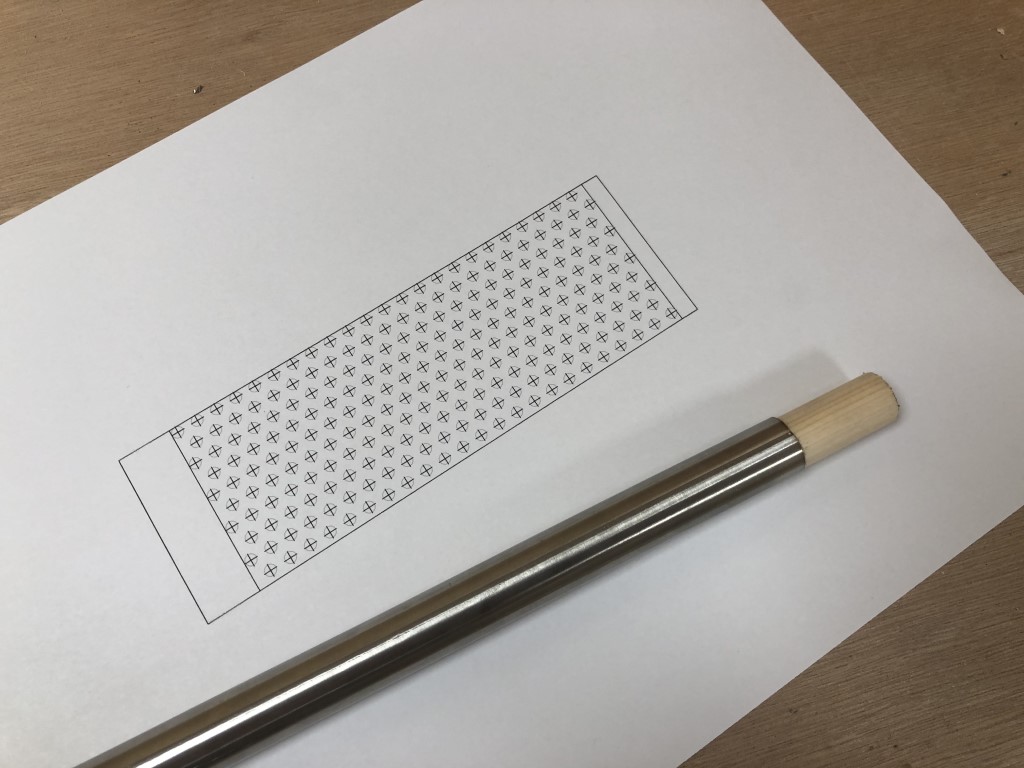
So, after drilling 460 holes with my column drill, some filing and sanding, I can say I’m rather proud of the result:
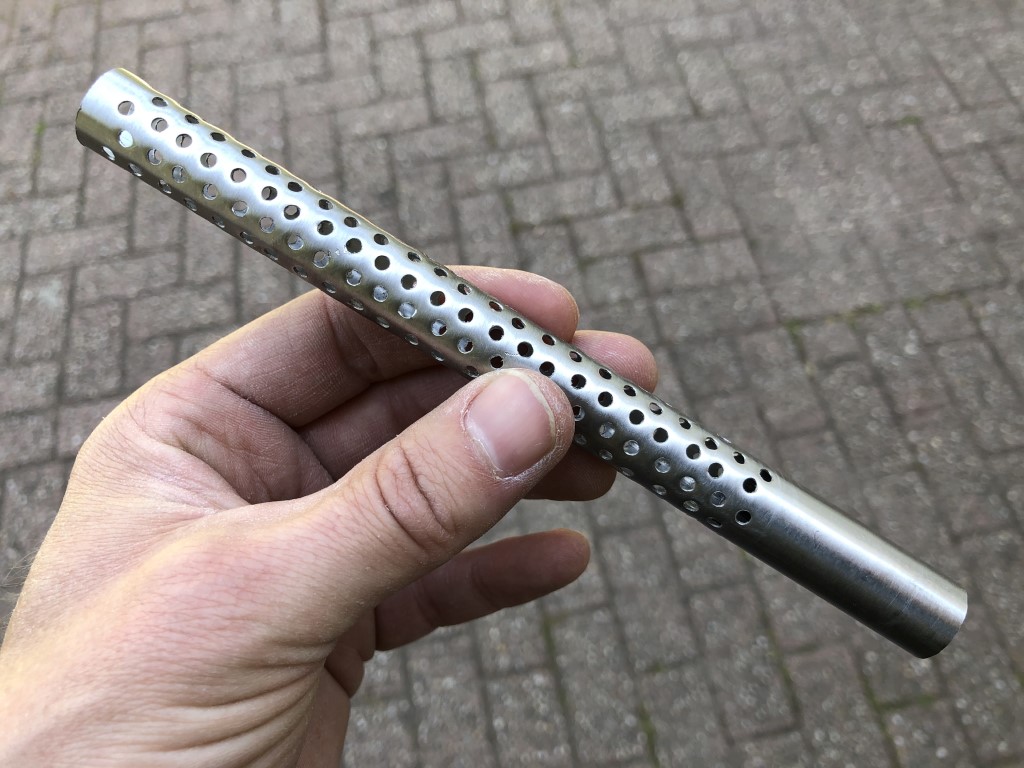
Next challenge: the exhaust pipe itself (outer wall). Buying a 40 mm stainless steel tube is easy, but they’re all 1.5 or 2 mm thick. We’ve tried to roll a 0.5 mm stainless steel sheet into a tube, which was doable, but TIG welding it turned out to be almost impossible (even with backing gas). Although a second attempt came out better, I’ve continued my search online for some ready made tubing. Hours into it, still no luck. Until I got the idea to search for a suitable thermos. And to my surprise I found a very small one that was just long enough. With an outer diameter of 45 mm it could very well be the case that the inner tube was about 40 mm wide. So I’ve ordered one and cut it open. Luck was on my side: the inner tube has a diameter of exactly 40 mm and the wall thickness is a beautiful 0.32 mm!!
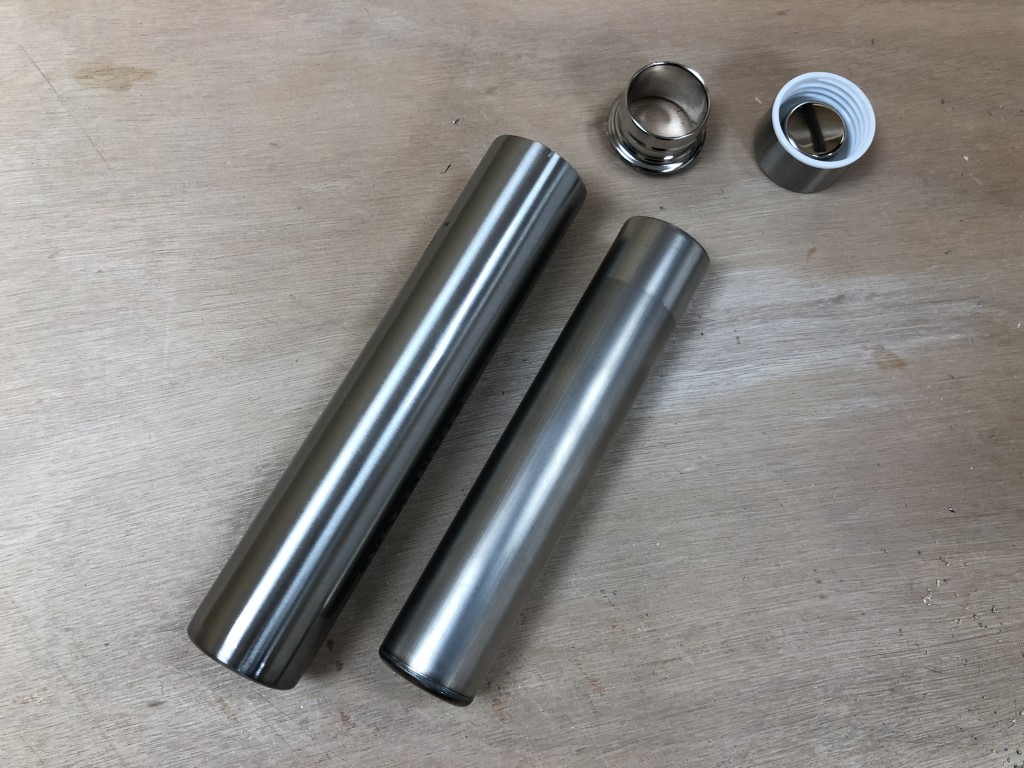
After that, I cut two disk out of 0.5 mm stainless steel sheeting, bringing it to the exact right dimensions with a lot of sanding and patience:
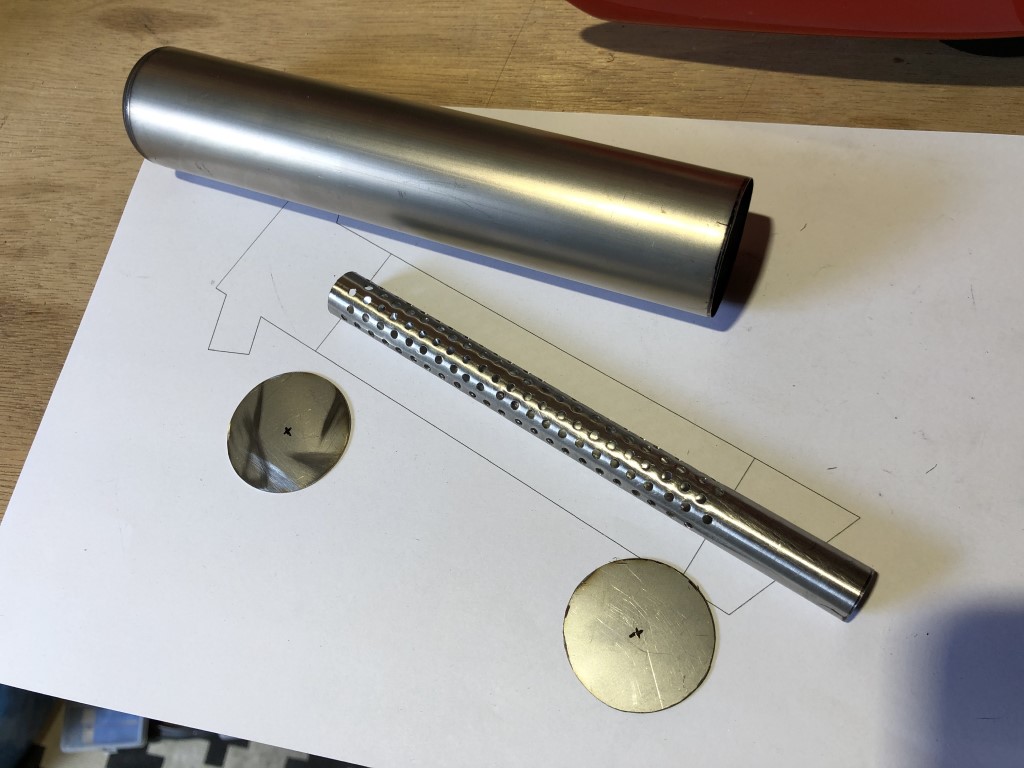
Then I cut 15 mm holes in the center (drilled undersized and carefully brought to 15 mm with a milling bit and some sanding). It’s coming together nicely up until now:
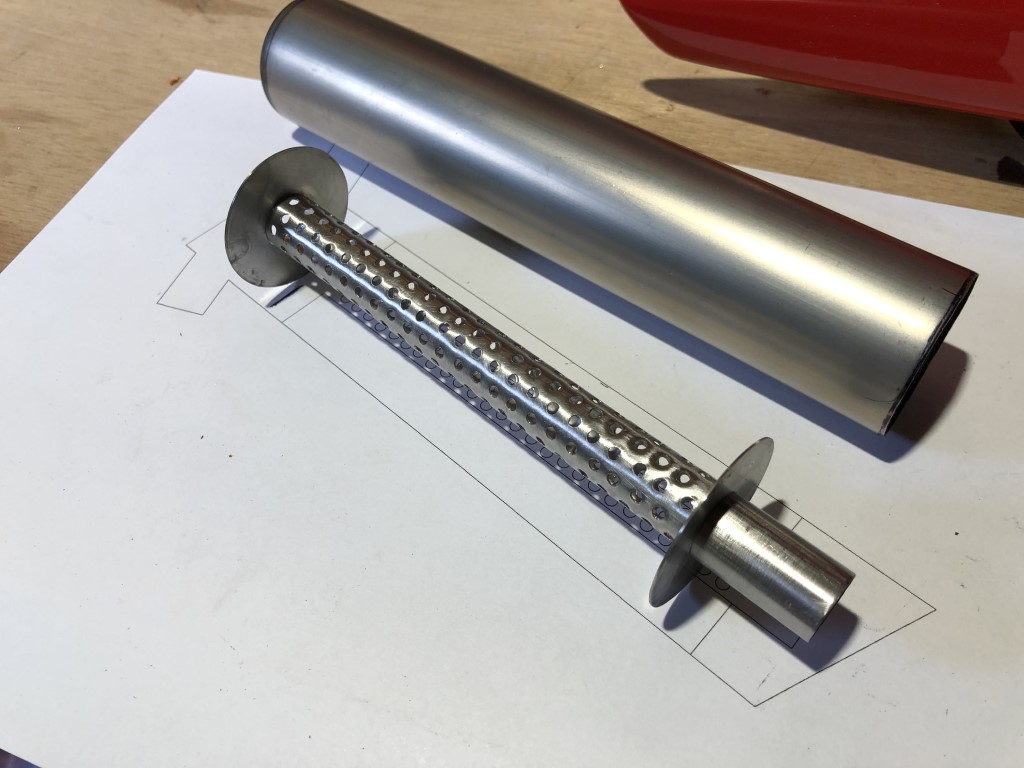
My fellow club member helped me out with hard-soldering the parts together, as I do not have the equipment or the skills to do so myself. Very grateful to have such supportive and attentive guys in our hobby!
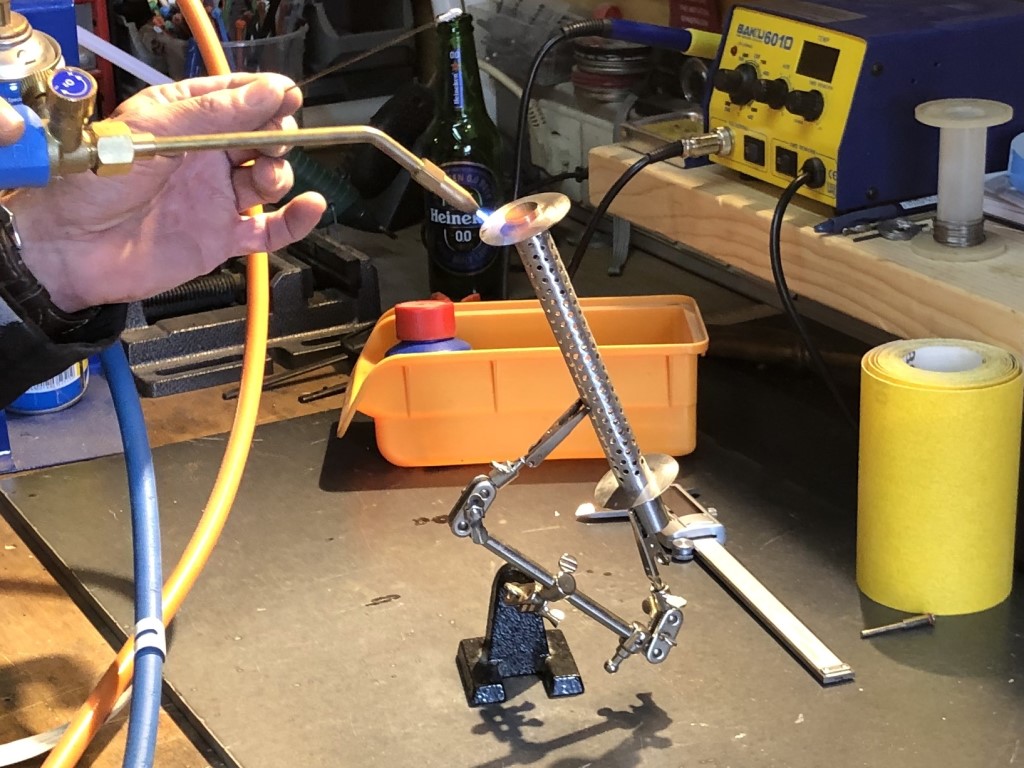
Lastly, I cut the open end of the scale exhaust at the right angle, and although I still have some sanding and shaping to do, it is already looking great:
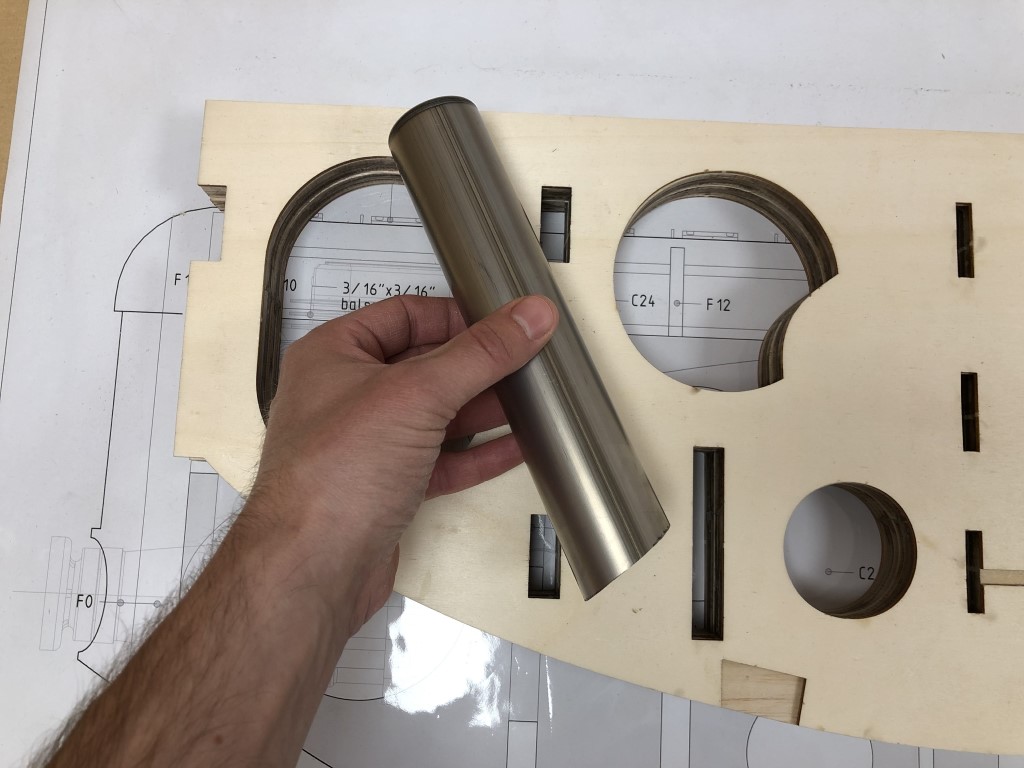
And this is what it looks like from underneath. The inner assembly still has to be soldered to the outside wall, but at least the fit is perfect already:
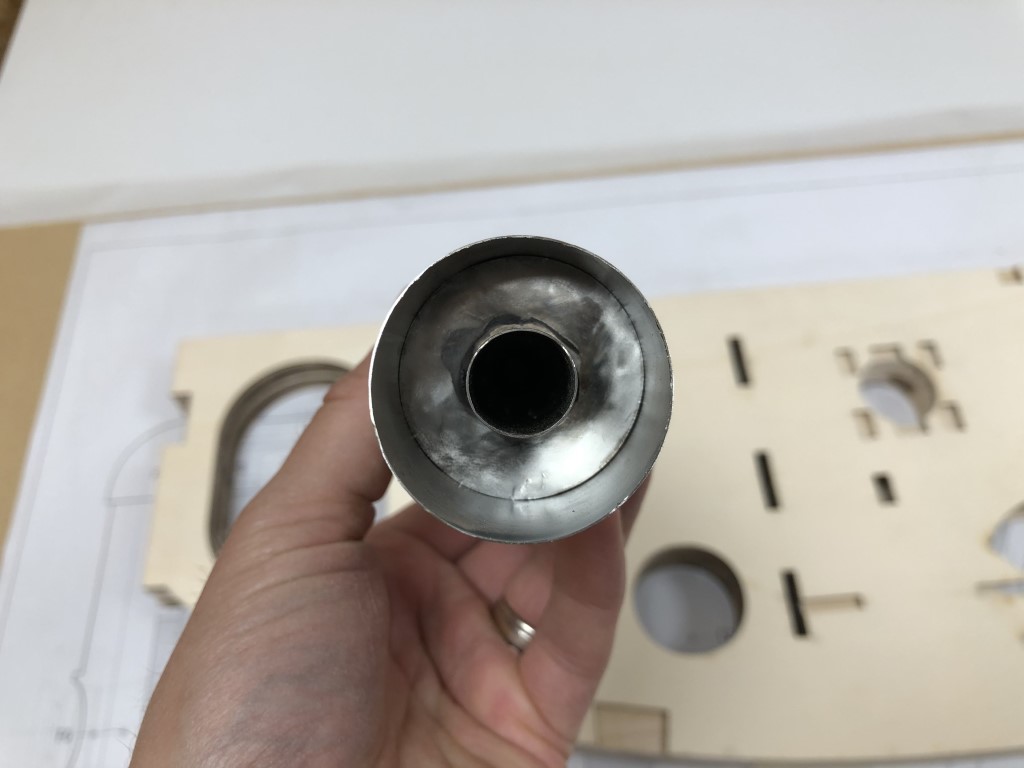
Here you can see the end of the pipe from an angle, shows nicely that the functional exhaust pipe is hidden in the outer tube. From the side, you wouldn’t tell it’s there and it sure has the appearance of the original scale exhaust:
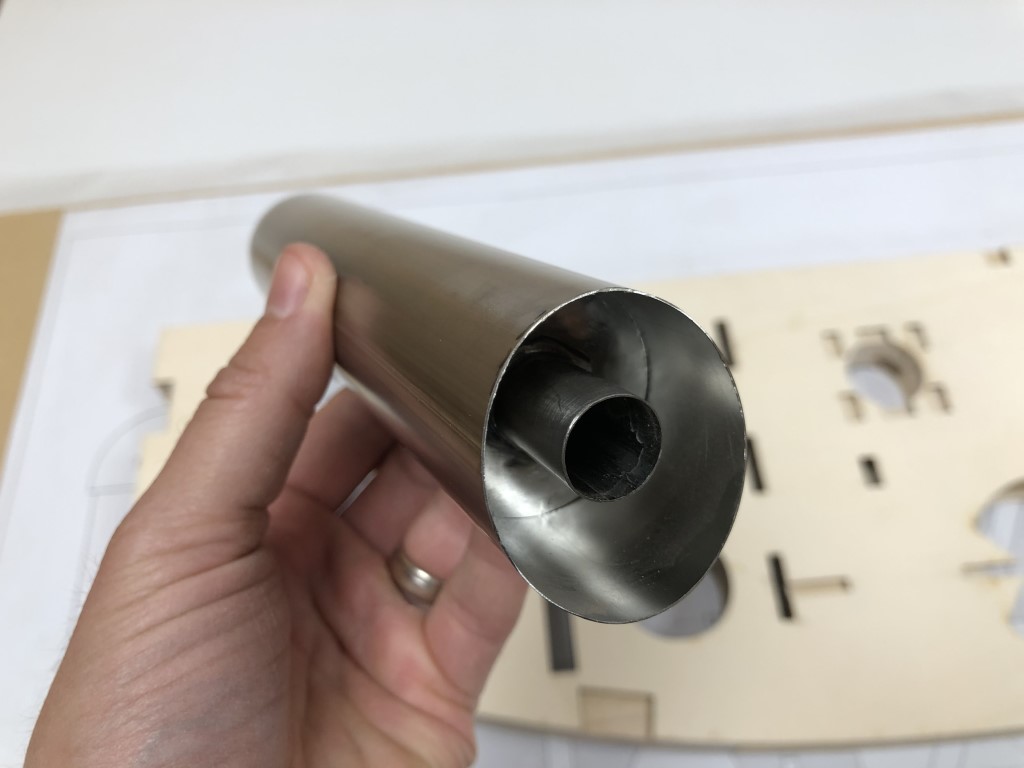
And this is what it’ll look like when it is fully finished and installed:
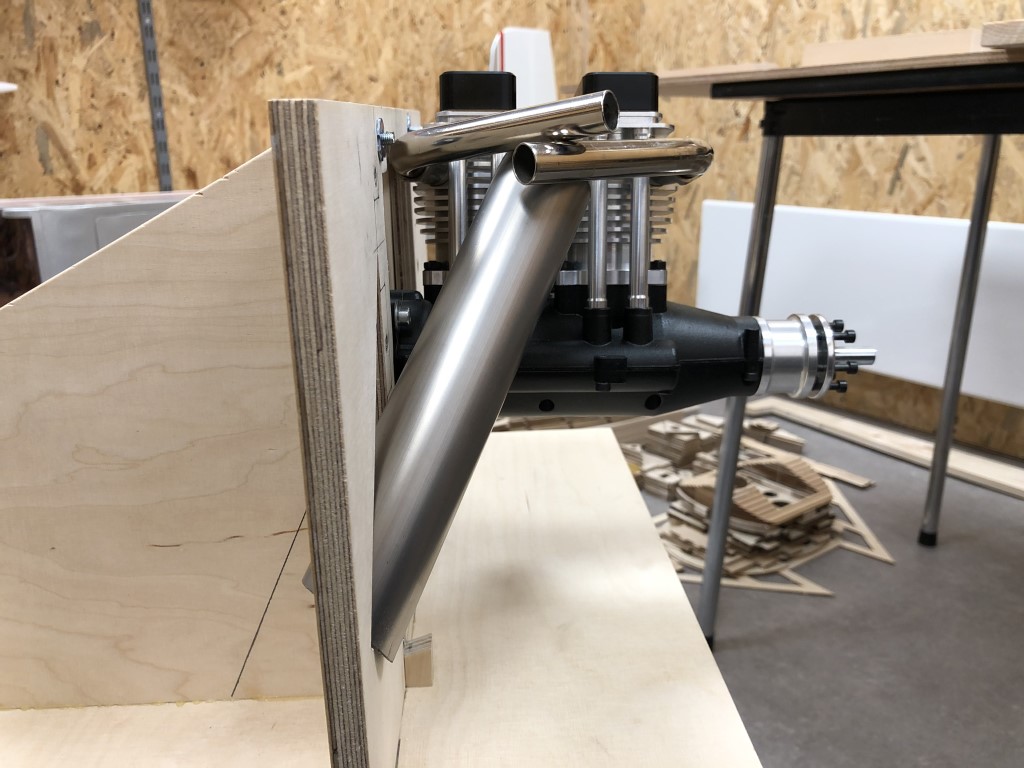
I also bought an extra cylinder exhaust tube from Roto, as it originally came with two different ones, sitting in different angles due to the different orientation of both cylinders. For me though, I want to bring them together in the center of the engine, so this seems easier to work with for my setup.
Now the challenge will be to create the transition from the original exhaust pipes to my custom muffler. Part of the challenge also is that the exhaust pipes attach to the cylinder heads using threads instead of being bolted on, which makes the geometry change while attaching it (the exhaust pipes point in the opposite direction) so I need to incorporate some flex tubing into my design. I hope it’s going to work out, because it would be totally awesome to have a working scale exhaust!
Here’s a small clip of the result up until now: